Few laboratory users spend much time thinking about their fume hood; despite the fact, it is quite arguably the single most important safety device found in the lab. Worse still, some fume hood operators and lab owners appear to treat the fume hood with contempt, disabling warning devices, removing sashes & airfoils and overcrowding with equipment.
Today’s fume hoods are the result of more than a century of development and are capable of providing excellent protection if selected, installed and used properly.
When selecting a new fume hood, lab designers and owners should consider the chemical compatibility required by the fume hood liner, the amount of workspace needed, the volume of exhaust airflow required, kind of plumbing and electrical services necessary, and so forth. An expert should always be consulted to help answer these important questions.
Location, Location, Location

While there are many installation considerations that fall beyond the scope of this article, the main issue that needs to be addressed once the hood reaches the laboratory installation stage, is the location. The fume hood must be located away from stray air currents. Any nearby air registers must be of a special low-velocity variety and the hood must not be located too close to doorways and operable windows. Before entering service, special on-site performance testing should be performed on the fume hood to demonstrate that its exhaust and supply air systems are all functioning correctly and providing the necessary performance. This test, known as the ASHRAE 110 test, uses tracer gas paired with sensitive testing equipment to measure the fume hood’s performance. This test also provides a baseline for future comparison with later test results.
Once the hood has been selected, installed and commissioned correctly and all of the contractors have gone away, it’s under the operational control of the lab owner and end user. This is where the safety chain usually breaks.
Maintenance is Key
As most lab operators are well aware, the main purpose of a fume hood is to capture, contain and exhaust fumes. It does this by drawing air around the operator and through the face of the fume hood. The fume hood is totally dependent on the airflow provided by the exhaust system. If this fails, the hood will provide no protection at all.
To ensure that hood operators know that adequate airflow is being supplied, all fume hoods must be equipped with a low flow alarm. Operators need to respect the alarm. When it sounds, they should lower the sash and wait several minutes for the airflow to be restored. If the alarm does not reset, the hood cannot be put back into operation until the root cause of the alarm has been identified. That is the only solution. The answer is not found by unplugging the alarm to disable it.
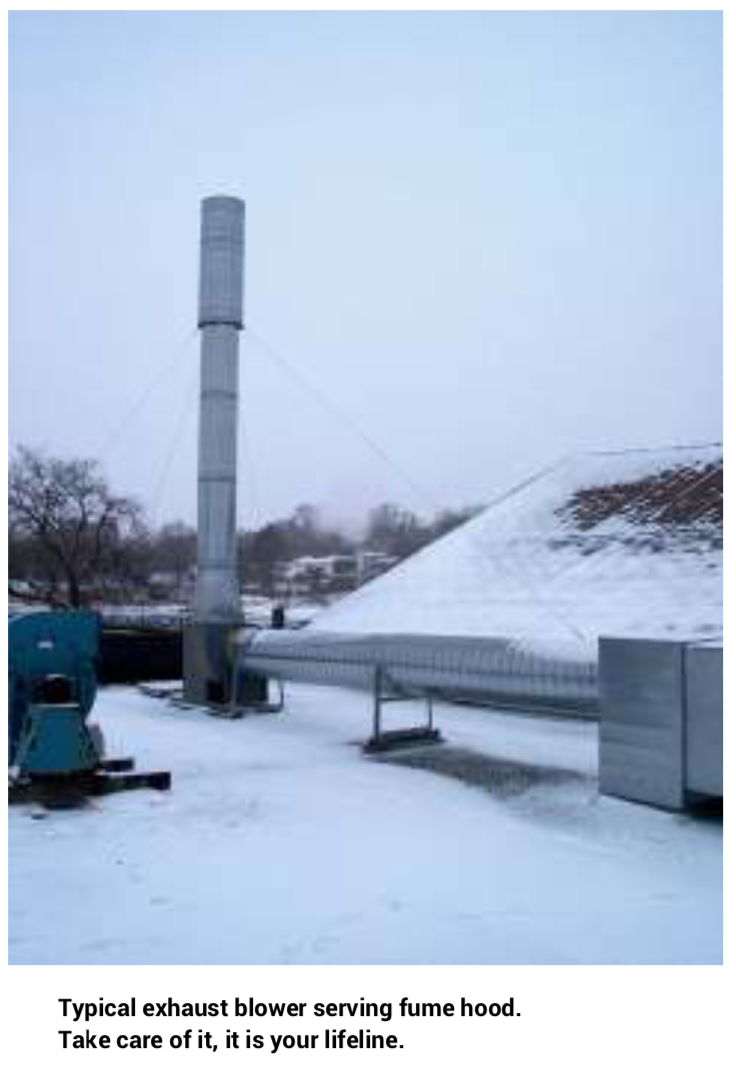
In order to avoid equipment failure and repeated alarms, preventative maintenance is the key. Maintenance staff is required to inspect and maintain the belts and bearings periodically, even if it means climbing to the roof of the laboratory. This preventative service is important.
One of the most important features of the fume hood for both safety and operation is the sash, which should be adjusted so that it is between the user’s face and the hazards. Sashes are usually made of tough safety glass and can provide significant protection in the event something goes wrong. Most hoods are designed to be used with the sash partially closed and provide only moderate fume containment with it fully open. There is a growing trend within the industry to install hoods, with a maximum sash working at sash height of 18 inches. In these instances, the sash should only be opened fully for setup and teardown of equipment. Operators should be aware that the hood does not offer much protection when it is fully opened. It should be equipped with labels indicating the maximum safe sash height.
Avoid Disrupting Flow
The inward movement of air that provides containment for the fume hood is actually at a very low velocity, typically 100 feet/minute. With ever climbing energy costs, the industry trend is currently toward developing hoods with even lower velocities of 60 fpm. While this may mean an energy savings, it can come at the price of safety as low velocities are easily disrupted. Generally, specially designed hoods are required for reliable operation at lower face velocities. Even with regular flow equipment, it is important for lab employees to walk slowly when near a fume hood. Even abrupt movements when working within the hood’s confines can cause materials to escape. When removing arms and other objects from the hood, operators should move them slowly backwards. They should also avoid making side-to-side movement or scooping motions.
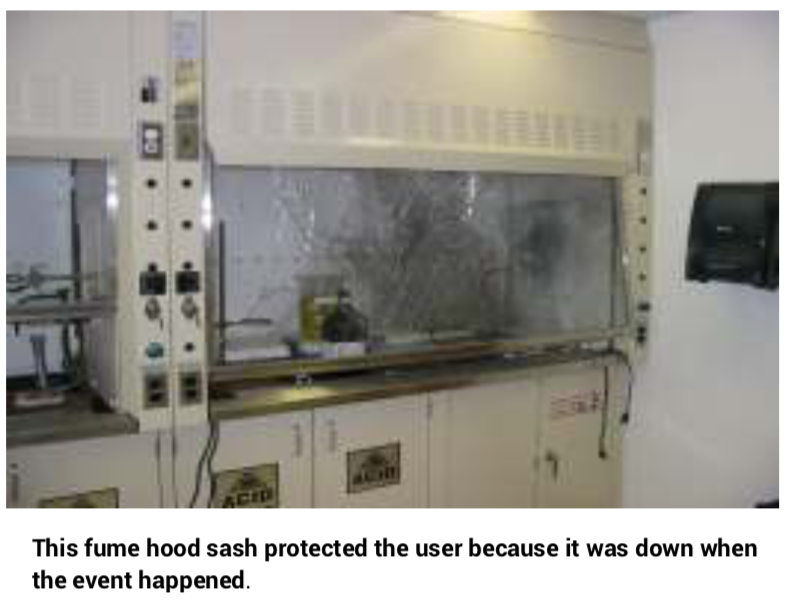
Large equipment placed in hoods has also been known to cause significant airflow disruption, leading to a loss of containment. This problem can be mitigated somewhat by installing items on several small blocks to allow airflow beneath. All objects should be placed at least six inches behind the sash.
Special Fume Hoods
There are special fume hoods constructed specifically for radioisotope and perchloric acid applications. While radioisotope hoods are similar to standard hoods, the liner is normally constructed from a smooth, cleanable stainless steel in order to facilitate decontamination. Perchloric acid hoods come equipped with a special water wash-down system used to remove condensate since perchloric acid produces dangerous explosive crystals, when vapours condense on the hood interior and ducting. Lab technicians should never perform perchloric work in a general-purpose hood.
Safety is Paramount
It’s important that fume hood performance be monitored and checked each year. It may have been sufficient in the past to simply measure the velocity of air entering at the hood face and compare with published requirements (usually 100 fpm). But in today’s safety-conscious world, it’s recommended that owners use the more stringent ASHRAE 110 tracer gas test.